Automation
Simplify Your Processes And Maximize Your Business
Automation
Automation is a big part of what we do at Morrisette Packaging. We are dedicated to investing in cutting-edge technology and equipment that streamline and automate the packaging process. By focusing on automation, we eliminate time-consuming tasks, allowing you to dedicate more time and resources to other crucial aspects of your business. Our team of in-house integrators and engineers works closely with you to design customized automation solutions tailored to your specific needs. We involve you in every step of the process, from budgeting and testing to evaluating ROI, ensuring transparency and collaboration. Our ultimate goal is to help you create the most efficient and productive version of your company through seamless automation.
-
Supply Chain Evaluation
Our diligent automation team analyzes and diagnoses your entire operation to uncover any potential gaps.
-
Equipment Integration
We identify which automation equipment suits your needs best and develop tailored solutions for your specific needs.
-
Equipment Service
After implementation, we continuously monitor your solution to ensure you receive maximized efficiency.
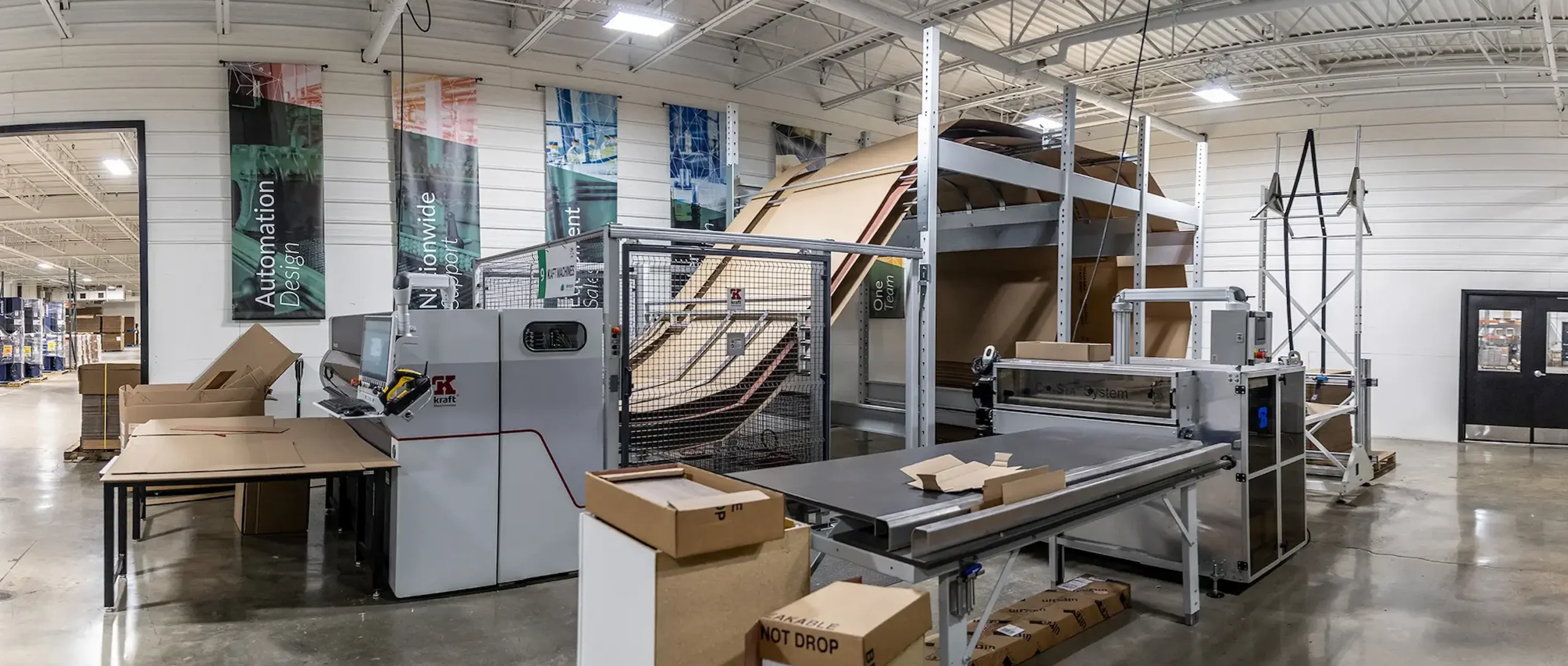
Automation Equipment With Solutions In Mind
Load Containment
Help protect your pallets as they
go out the door and throughout the transit process.
Case Erecting & Sealing
Reduce unnecessary labor and create uniformity in how your cases look – every time.
Shrink Packaging Systems
From simple jobs to the more complex, we have the shrink packaging equipment to fit your needs.
Protective Packaging Systems
We have void fill and cushioning solutions to keep your product safe, no matter where it goes.
Flexible Packaging Systems
Our bagging, form fill, and seal equipment keep your options for packaging flexible and adaptable.
Coding & Labeling
Make your mark count. Our experts will assist in finding an automated labeling solution for you.
Robotics
State-of-the-art equipment that provides reliability and nimbleness in pick & pack/palletization applications.
Conveyance & Integration
Our in-house integrators have the experience to tailor conveyor systems to meet any spatial requirements.
Your Success Is Our Success
Automation in packaging “reduces both the costs and prices of goods and services,” and can increase productivity by as much as 233%.
Automation can also help reduce excess packaging waste that can cost hundreds of thousands of dollars every year.
Morrisette Packaging’s patented Shrink Smart automation technology eliminates tail end waste commonly involved in shrink wrapping upholstery; saving manufacturers big money with one simple solution.