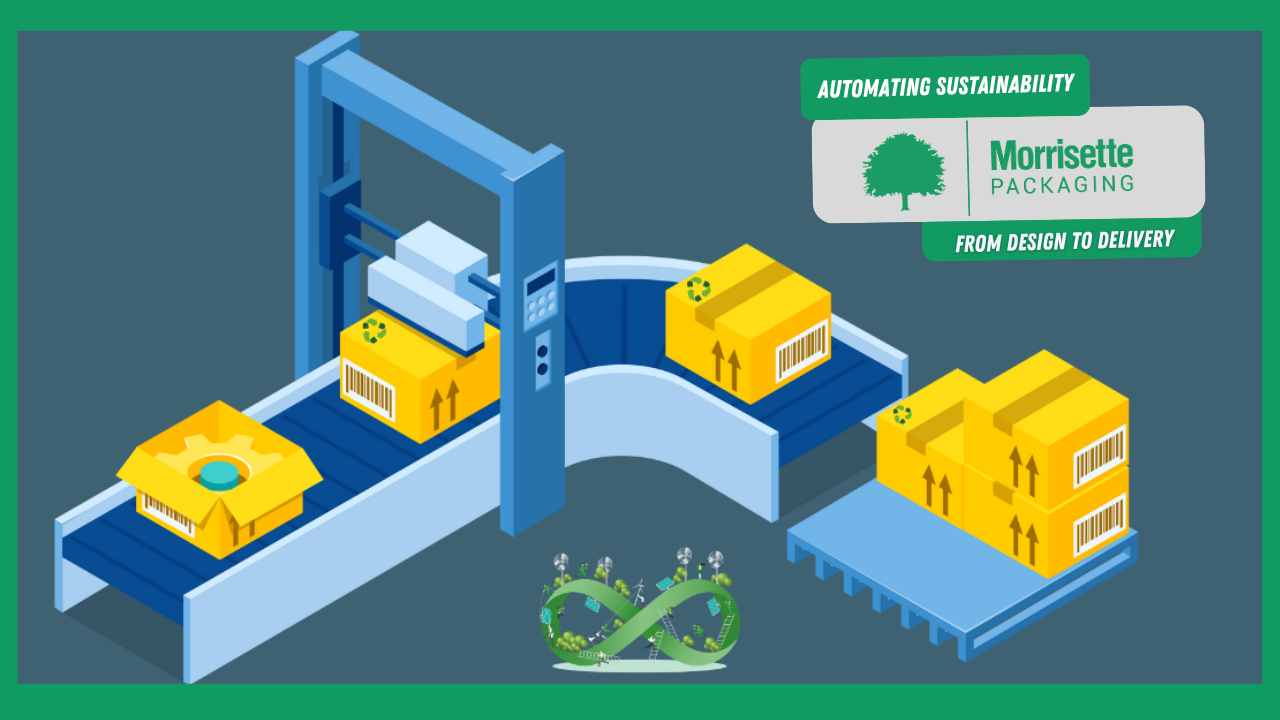
Automating Sustainability
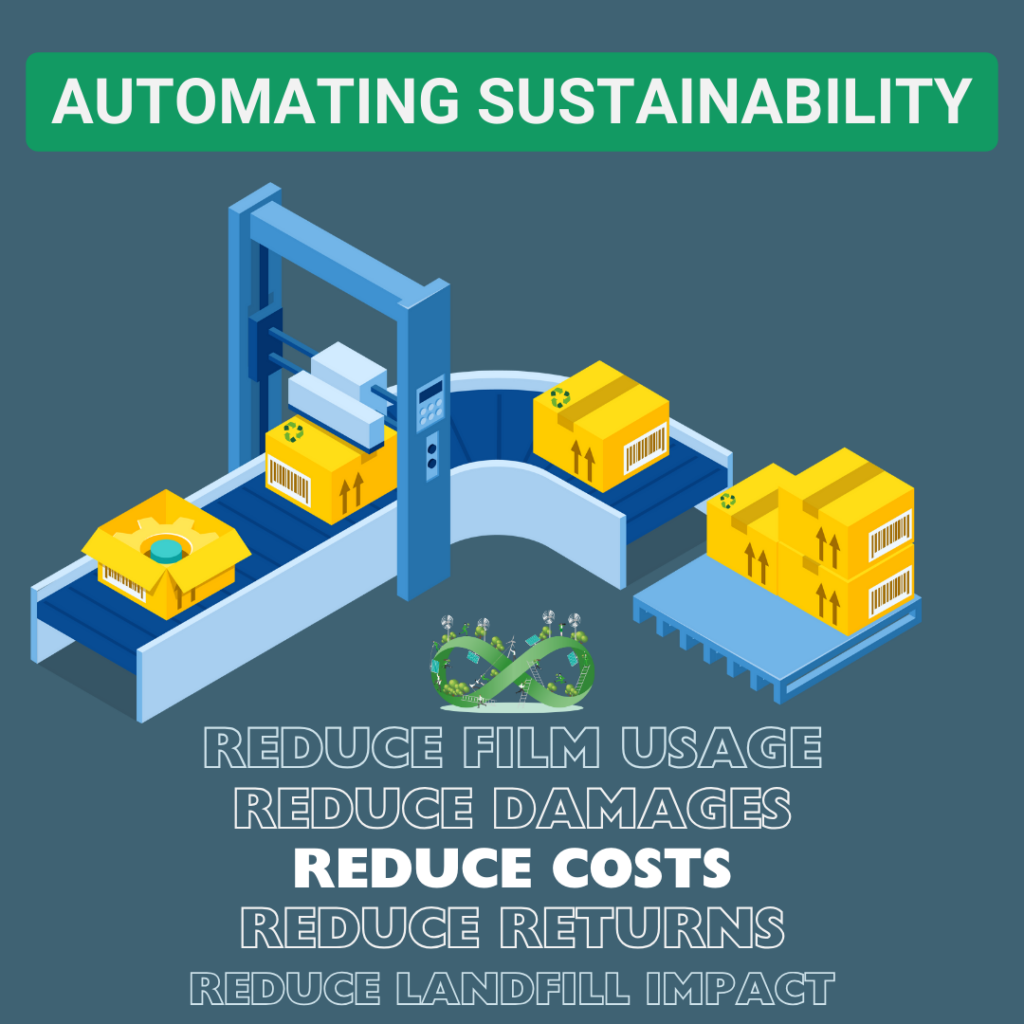
As the push for sustainable packaging grows alongside consumer and regulatory demand for it, the natural reaction may be to avoid the extra time, effort, and resources moving to a more sustainable solution may require.
How do you meet the mounting demands to achieve certain sustainability benchmarks wihtin your company?
Automated packaging systems help you save time and money while simultaneously reducing waste and increasing your sustainable packaging initiative.
Packaging Automation Equipment & Sustainability
In the video above, Morrisette Packaging’s Packaging Equipment Engineer, Greyson Taylor, gives a thorough walkthrough on how the Lantech QL-400 reduces waste, saves costs, and promotes a greener future.
Lantech is a premier automation partner for Morrisette Packaging. Our automation engineers understand Lantech’s offerings and how to make your various processes more efficient
Can an automation system help address your company’s sustainability initiatives?
Absolutely.
Choosing the right packaging automation equipment and system helps you:
- Reduce Film Usage
- Reduce Product Damage
- Reduce Returned Goods
- Reduce Landfill Impact
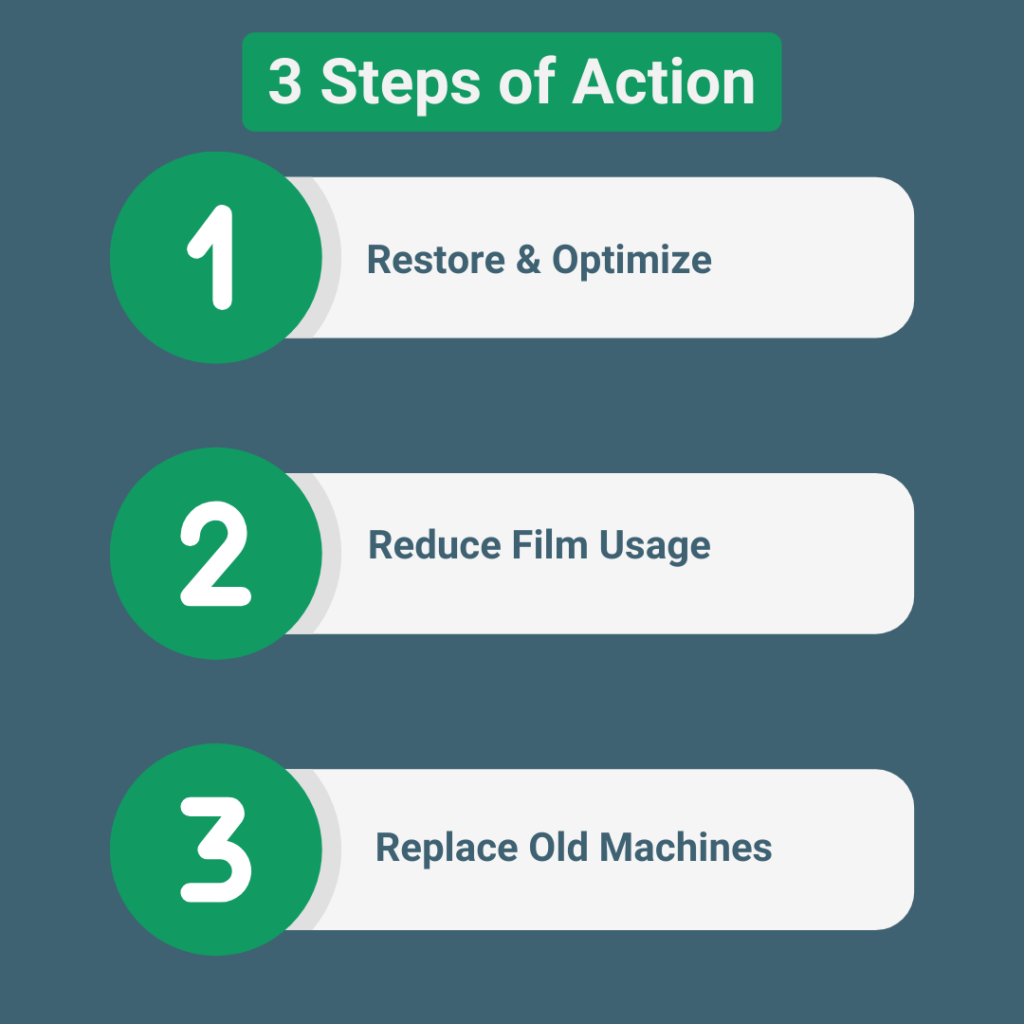
Lantech has outlined 3 Actionable Steps that a packaging automation system delivers to help you achieve your sustainable packaging goals:
1. Restore & optimize existing equipment.
- Return stretch wrappers to fully functional condition by ensuring film delivery system and pre-stretch are working to full potential.
- Optimize wrap profile for required containment force and load type to create safe-to-ship loads at the lowest film usage. Then, create stretch wrapping standards and put a process in place to ensure it is adhered to.
- Aim for optimal Containment Force without increasing film breaks. Film breaks encourage operators to “tweak” the machine, causing deviations from standards, impacting load quality and increasing film usage.
- Add options in the field to improve the performance of existing Q Semis:
- Where possible, increase pre-stretch levels to optimize the potential of premium-grade stretch films
- Add Pallet Grip® to keep loads locked to the pallet and help reduce transit failure/damage
2. Reduce film usage by boosting its performance.
- Half of all the stretch film sold in the U.S. is still hand wrap. Q Series semi-automatic stretch wrappers can reduce film usage by well over 50%.
- Without putting product at risk or increasing damage/returned goods
- Optimize wrapper settings, pre-stretch levels and wrap profiles to gain full potential of stretch films
- Most premium-grade films can be stretched by 225% or more.
Standard pre-stretch on Q300 series is 200%.
Standard pre-stretch on QL400 series is 250%.
3. Replace old machines with new wrapping technology.
- The Q Series Film Delivery System is designed to maintain pre-stretch levels.
- The QL400 series includes Load Guardian technology that maintains and delivers profile integrity with correct containment force.
- Ensures every operator can wrap the same load the same way.
- Ensures enough Containment Force for safe-to-ship loads.
- The QL400 series comes standard with Pallet Grip.
- Locks loads to pallets during transit and reduces damage and returned goods
- Damage and returned goods increase waste that has to be disposed of and increase carbon footprint by more than 3X:
- 1X: Original primary packaging, stretch wrap, and original freight
- 2X: Return freight
- 3X: Rework, new primary packaging, new stretch film and 3rd freight