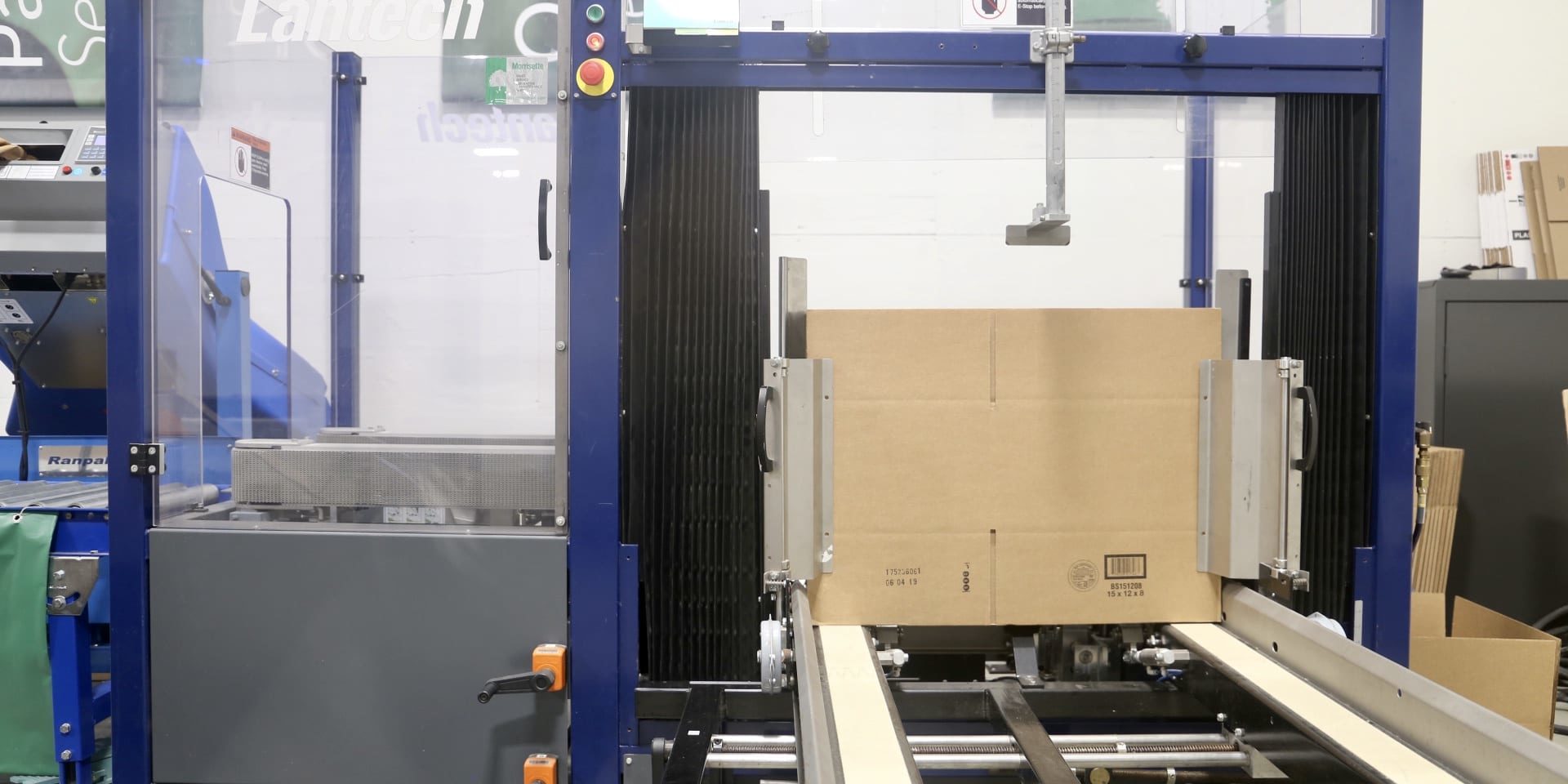
WHY NOW IS THE TIME FOR CASE FLOW EQUIPMENT
Your business is anchored to your ability to move your products through your warehouse and out the door to the customer. If you have more than two workers handling case forming, it’s likely time for some type of equipment to support your case flow process.
Companies rely on case flow systems to effectively prepare cases for shipment:
- Case erecting and forming
- Case packing
- Case sealing
- Case labeling
- Product palletization
Why should you automate?
In today’s demanding warehouse environments, there has never been a higher desire for flexible solutions. What’s needed today may not be needed tomorrow; and manufacturers need to be able to make swift changes. Conserving time and money is essential in a warehouse. Automating the case flow process is one way to save both – and have a professionally packed case.
Many of the equipment options that are available for case forming have fast change-over abilities. They are also designed to grow with your business and handle the capacity of your production – no matter how big or small.
Reduction of damages is another reason companies rely on automation. Machines are able to achieve a perfect box every time. Having properly erected cases is essential for keeping your packaging line running efficiently and your product safe throughout transit. According to Lantech: “If you have 90 degree corners, you have 30% more stacking strength! In this way, you prevent the cases at the bottom from being crushed and the case and contents from becoming damaged.”
As with all innovations and technology advancements, we have also seen packaging equipment become a more economical choice for companies of all sizes. Couple this with the fact that there are exponentially more options available now than a decade ago, the widespread use of equipment for the case flow process is timely.
Step 1: Case Forming
Case erecting and forming machines take flat cartons and automatically form, fold, and seal the bottom of the carton. Like most equipment options, there are a variety of options, ranging from semi-automated to fully automated.
Our reliable case forming equipment options offer throughput speeds up to 30 boxes per minute. Modular machines are available for special applications where you can configure the case forming machine for your application needs.
If a fully automated system is not right for your production volume, a common solution is semi-automated systems that use a combination of human efforts and machine efforts. Ultimately any case forming equipment is going to take you one step closer to reducing damages and increasing efficiency.
Step 2: Case Packing
Case packaging (or case filling) equipment is the next step in the case flow process. Packing equipment can be integrated with your case forming equipment, and is available in a variety of loading configurations. There is a case packing solution available for just about anything you want to put in a box.
Companies often turn to case packing equipment when production grows beyond what the workforce can handle. If you are dealing with a lot of different SKUs and order types, you can benefit from durable case packing equipment that can easily adapt to changing order types.
Step 3: Case Sealing
After the products are packed into the box, case sealing equipment is used to adhere the box with either tape or adhesive. One of the number one benefits of automating the case sealing process is reduction in waste of materials from using too much tape during manual sealing. At the same time, you can trust that you have the exact right amount of sealing material and your products will be safe in the package.
If you are going to be sealing boxes of different sizes, make sure you select a random case sealer, which will adjust based on the length of each case. Uniform case sealers are the preferred option for companies that have large runs with the same size case.
A few other considerations include the packaging environment (in regard to the temperature and humidity) and the weight of the product (as some machines have maximum weight capacities).
Step 4: Case Labeling
Today’s case labeling equipment options are faster and more advanced than ever before. At this stage of the packaging process, it’s most important that the information on the label is accurate, durable, and legible so that it can get to the customer.
Your case labeling equipment can also be integrated with your case sealer to save time and create one cohesive system. This advanced technology can be programmed to print and adhere labels for barcodes, important product information, and more.
Step 5: Product Palletization
Creating a secure pallet can be a dangerous part of the packaging process. Palletizers are machines that are used to stack cases on a pallet. Using palletizing equipment reduces the physical burden on your workers. It also eliminates the need to attract enough labor to keep operations running. This is where machines and robots become essential.
Many companies are choosing stretch wrap to secure their pallets. When this is the case, there is also an opportunity for integrated equipment that can both palletize and stretch wrap.
Talk to An Equipment Specialist
There are a lot of factors that go into deciding which equipment is right for your current operations and growth projections. Talk to a Morrisette Automation Specialist to get all of your packaging equipment questions answered.