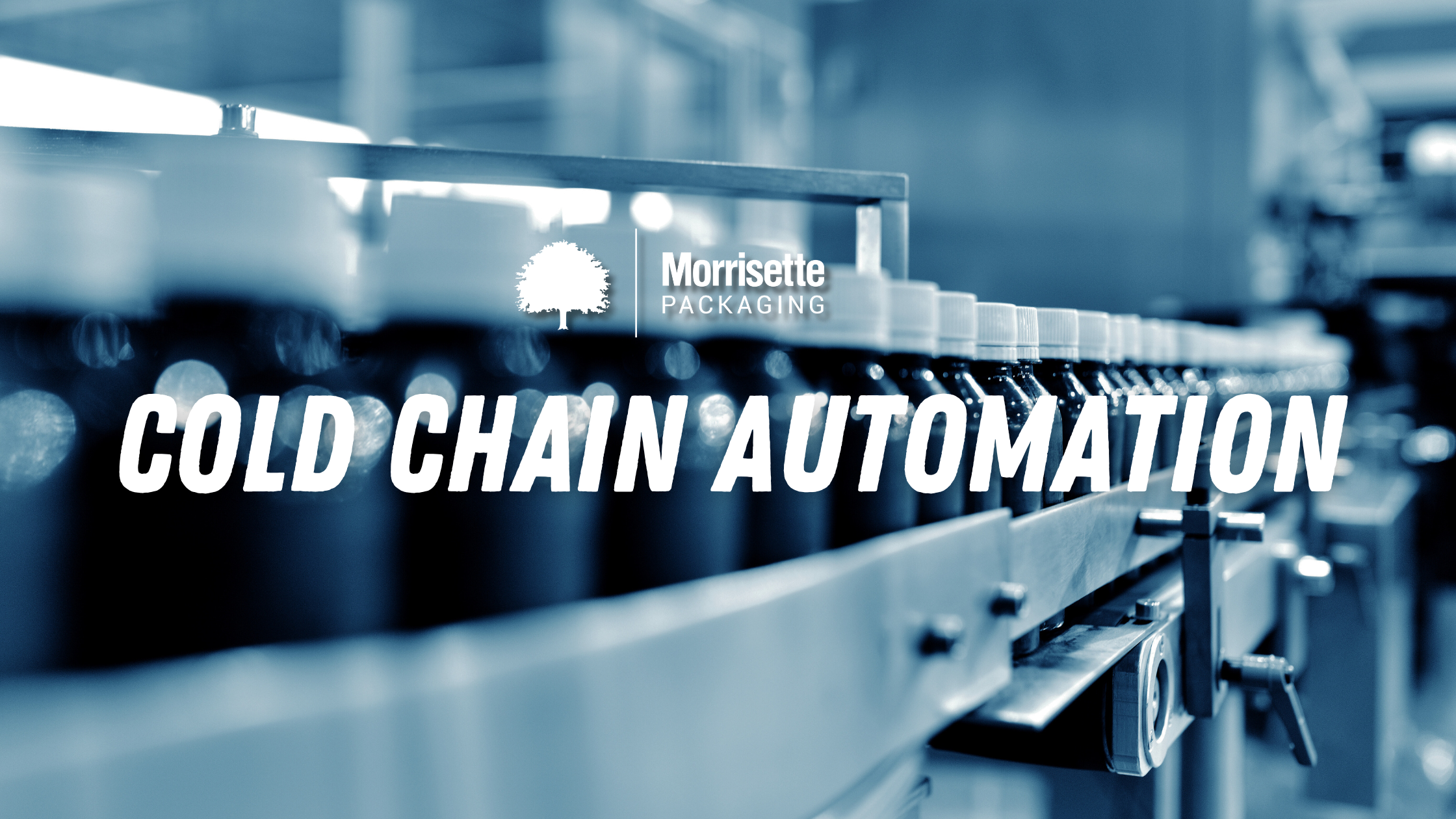
AUTOMATION IN COLD CHAIN PACKAGING
Introduction to Cold Chain Packaging
In the fast-paced world of packaging, speed and efficiency are paramount. Ensuring a “perfect seal” and maintaining precise temperature conditions are critical challenges, especially for industries that rely on cold chain packaging.
What is cold chain packaging?
Cold chain packaging is a system of materials and methods that keep temperature-sensitive products at the right temperature. This packaging is used to store and transport products like food, medicine, and vaccines.
Cold chain packaging, also known as temperature-controlled packaging, refers to the specialized process of storing and transporting goods within a specific temperature range. This includes refrigerated and frozen products, as well as items that must be kept at stable ambient temperatures to prevent degradation. Industries such as food and beverage, pharmaceuticals, chemicals, and personal care rely on cold chain packaging to maintain product quality and compliance with safety regulations.
The cold chain process involves several key components:
- Packaging: Insulated and refrigerated solutions to maintain product temperature.
- Storage: Temperature-controlled environments, such as cold storage warehouses.
- Transportation: Refrigerated trucks, railcars, and containers.
- Handling: Optimized loading and unloading procedures to prevent temperature fluctuations.
Maintaining efficiency at each stage of the cold chain is essential to avoid spoilage, ensure compliance, and protect consumer health.
Automation is transforming temperature-controlled packaging by enhancing efficiency, reducing errors, and improving compliance with strict industry regulations. Companies that integrate packaging automation into their cold chain logistics gain a competitive edge by ensuring product integrity and streamlining operations.
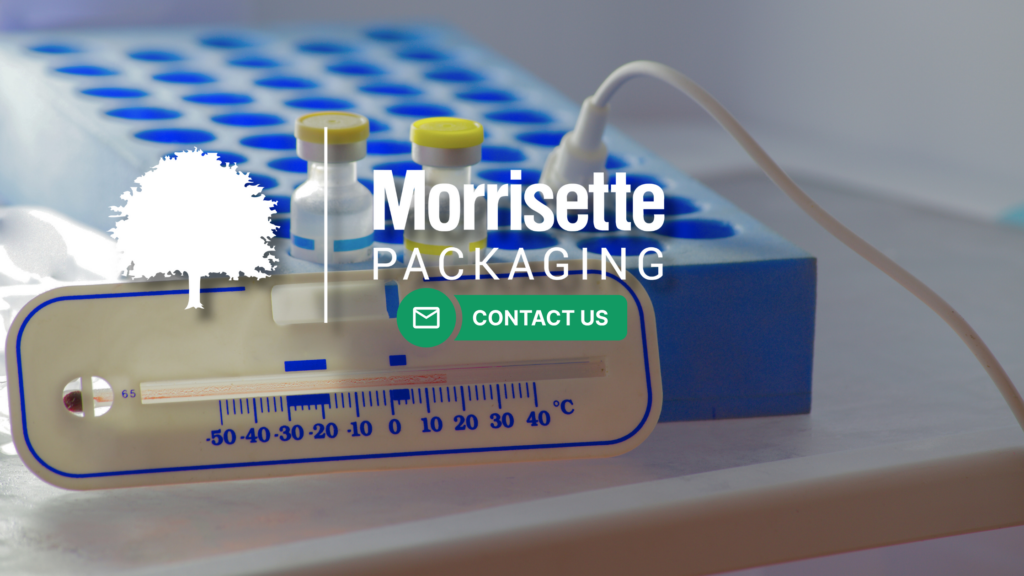
The Role of Automation in Cold Chain Packaging
Automation plays a crucial role in enhancing the efficiency and reliability of temperature-controlled packaging. In cold chain and temperature-controlled packaging, traceability is paramount.
Cold Chain Packaging is all about proving the product stayed cold.
Automated RFID readers or 6-sided barcode scanners that can track where a product is and for how long can save a ton of time and labor when automated.
By integrating advanced machinery, robotics, and digital monitoring systems, companies can streamline their cold chain logistics while minimizing human error.
1. Automated Form, Fill, and Seal (FFS) Machines
FFS machines are essential for high-speed, high-volume packaging operations. They ensure a consistent and secure seal, preventing contamination and temperature deviations. Automated FFS systems help optimize production by reducing transition times and increasing output while maintaining precision.
2. Automated Coding and Labeling
Proper labeling is crucial in cold chain packaging. Automated coding systems apply expiration dates, batch numbers, and tracking information directly onto packaging with precision. Many systems use continuous inkjet (CIJ) printing, where electrically charged ink droplets are precisely applied to packaging. This ensures that essential product information remains visible and legible throughout distribution.
3. Temperature Monitoring and Real-Time Alerts
Automated temperature monitoring systems use advanced sensors to track conditions inside packaging, warehouses, and transport containers. These sensors provide real-time data, helping companies detect fluctuations that could compromise product integrity. If deviations occur, automated alerts trigger corrective actions to mitigate risks before they escalate.
4. Automated Storage and Retrieval Systems (AS/RS)
AS/RS technology optimizes warehouse operations by automating the movement of temperature-sensitive goods. These systems reduce the need for manual handling, ensuring products remain within their required temperature range. Additionally, AS/RS helps prevent inefficiencies and errors in inventory management, leading to faster order fulfillment and reduced waste.
5. Robotics and Conveyor Systems
In cold storage environments, robotic automation reduces the need for human labor in extreme temperature conditions. Automated conveyors and autonomous mobile robots (AMRs) improve material handling, accelerating the movement of goods within facilities while maintaining proper storage temperatures.
As a Rolling on Interoll partner, Morrisette Packaging is well-positioned to help you refine your process.
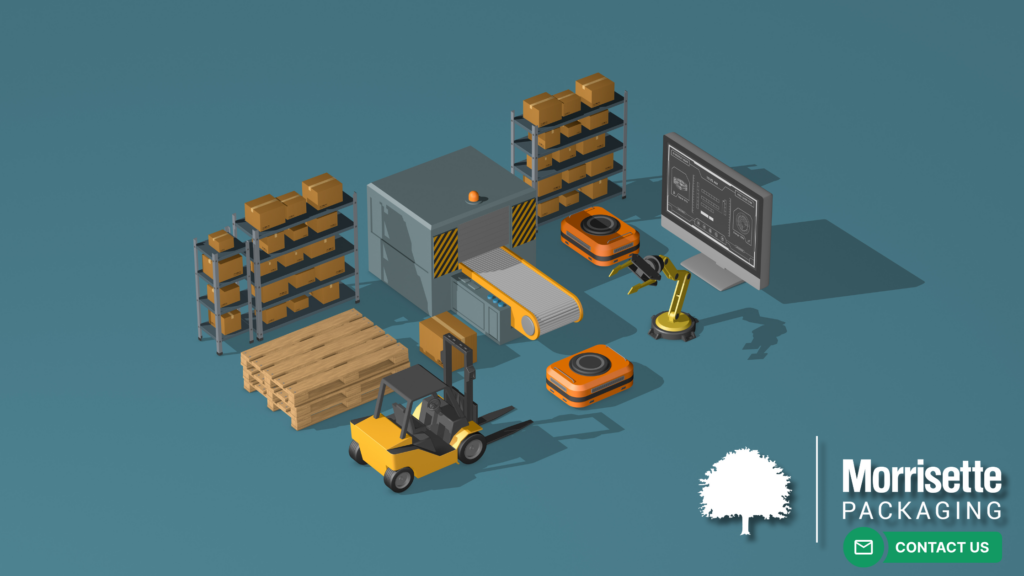
The Benefits of Cold Chain Packaging Automation
Automation in cold chain logistics provides numerous advantages, including:
Enhanced Product Safety and Quality
Maintaining precise temperature conditions is vital for preventing spoilage and ensuring product efficacy. Automated systems improve accuracy in monitoring and controlling temperatures, reducing the risk of deviations that could lead to product degradation or contamination.
Increased Efficiency and Reduced Costs
Automated cold chain solutions operate 24/7, improving throughput and reducing manual labor requirements. This leads to cost savings in operations, fewer product losses due to spoilage, and a more reliable supply chain.
Regulatory Compliance and Traceability
Industries such as pharmaceuticals and food manufacturing are subject to stringent safety regulations. Automated tracking and temperature monitoring provide comprehensive data logs, ensuring compliance with regulatory standards and enabling efficient product recalls if necessary.
As demand for temperature-sensitive products grows, automation allows businesses to scale their operations efficiently. Whether handling seasonal fluctuations or expanding into new markets, automated cold chain packaging systems provide the flexibility needed to adjust production and distribution capacity.
The Future of Cold Chain Packaging with Automation
As industries continue to embrace cold chain packaging automation, the focus on innovation will drive even greater efficiencies. Emerging technologies will further revolutionize the industry.
Morrisette Packaging is at the forefront of cold chain packaging and packaging automation solutions. Our team helps businesses evaluate and implement state-of-the-art packaging technology to meet regulatory requirements, enhance efficiency, and protect product quality.
Contact us today for a free consultation.